Unsere Ressourcen
ETESIA verfügt über Produktionsanlagen, die auf dem neusten technologischen Stand sind. Diese werden im Sinne der Strategie Qualität-Sicherheit-Umwelt eingesetzt und sind darauf ausgerichtet, die Prozesse zu Gunsten des Menschen, des Unternehmens und der Natur zu verbessern. So respektiert unser gesamter Produktionsprozess internationale Qualitätsmanagementnormen. Dies ist ein Garant für die Qualität unserer Produkte und schließt die computergestützte Fertigung mit ein.
Die ETESIA Abteilungen
Bereich Technik
Die Abteilung Technik besteht aus ca. 90 Mitarbeitern, die sich in 10 Abteilungen aufgliedern: F+ E, Einkauf, Methoden und Industrialisierung, die Montage, die Blechbearbeitung, Instandhaltung, Qualitätskontrolle, Logistik, Wareneingang und Versand. Eine gemeinsame Datenbank gestattet, das alle Zugriffsberechtigten technische Informationen in Echtzeit aktualisieren können, so dass die Termintreue optimiert werden kann.
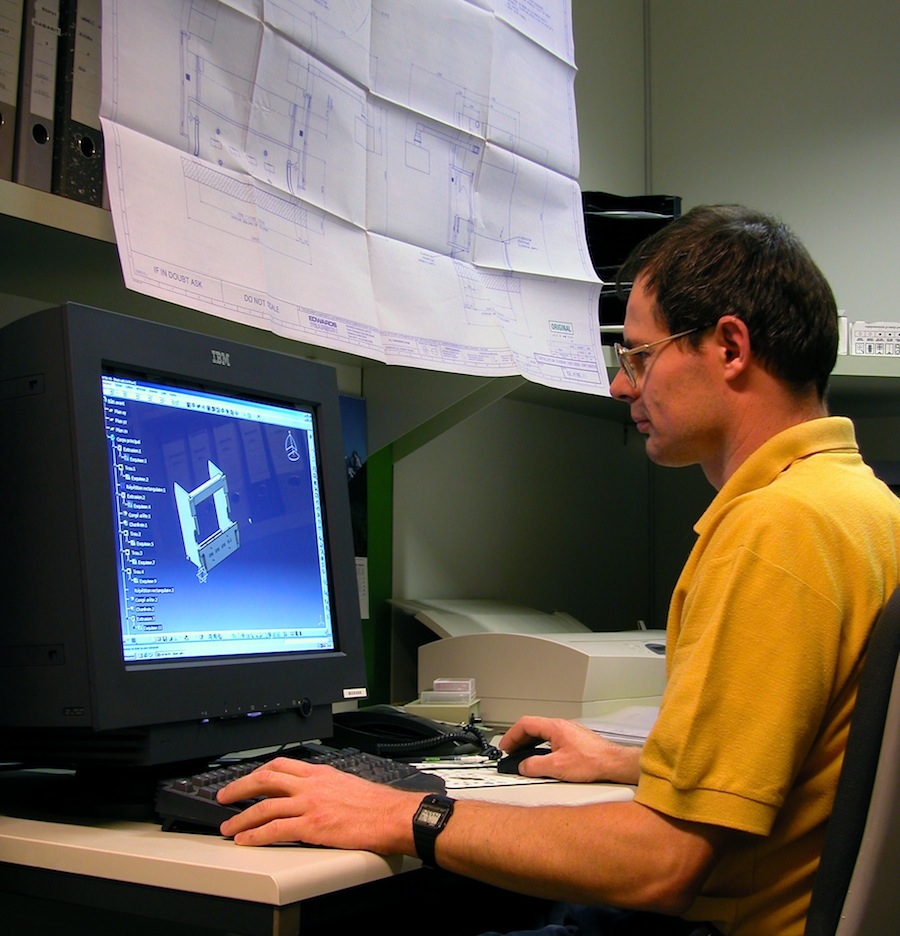
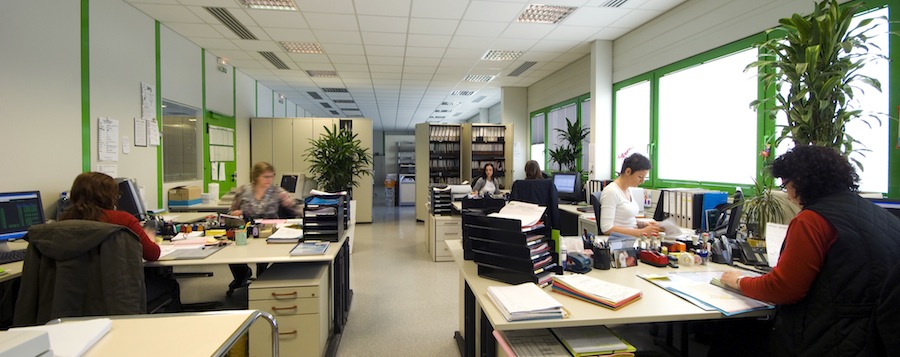
Kaufmännischer Bereich und Marketing
Der kaufmännische Bereich untergliedert sich in 3 Abteilungen, die für unsere Vertriebshändler und Endkunden zuständig sind: kaufmännische Abteilung, Marketing und Kundendienst.
Die beiden erstgenannten Abteilungen umfassen am Standort Wissembourg 12 Mitarbeiter, die eng mit unserem Distributionsnetz und unseren Vertriebsleuten zusammenarbeiten. Das Vertriebsnetz besteht aus ca. 30 Vertretern, die in ganz Europa präsent sind: Frankreich, Großbritannien, Deutschland, Benelux-Staaten, Italien, Spanien, Portugal ...
Kundennähe, Erfassen der Wünsche und Serviceleistungen sind für uns die wichtigsten Verhaltensregeln im Umgang mit unseren Händlern und Endkunden.
Bereich Kundendienst
4 Kundendienst-Techniker, 1 Verantwortlicher für das Ersatzteillager, 4 Bestellbearbeiter, 2 Mechaniker für Reparaturen, 1 Sekretärin und 1 Serviceverantwortlicher kümmern sich mit Hingabe um die Händler und Endkunden von ETESIA.
Einige Kennzahlen: jährliche Schulung von 700 Kunden auf 9 Sprachen, 15000 Kundenanrufe jährlich und mehr als 200 000 Ersatzteilbestellungen pro Jahr.
Erfassen der Kundenwünsche, Beratung, Reaktionsschnelle und Verfügbarkeit - das sind die Schlüsselwörter des Kundendienstes bei ETESIA.
Produktionsanlagen
ETESIA verfügt über Produktionsanlagen, die auf dem neusten technologischen Stand sind. Diese werden im Sinne der Strategie Qualität-Sicherheit-Umwelt eingesetzt und sind darauf ausgerichtet, die Prozesse zu Gunsten des Menschen, des Unternehmens und der Natur zu verbessern. So respektiert unser gesamter Produktionsprozess internationale Qualitätsmanagementnormen. Dies ist ein Garant für die Qualität unserer Produkte und schließt die computergestützte Fertigung mit ein.
Blechbearbeitung
In der Blechbearbeitungswerkstatt werden alle Stahlblechteile und fast alle maschinengeschweißten Komponenten (Fahrgestell, Rahmen usw.) hergestellt. Die Produktionsstätte verfügt über zwei Blechbearbeitungsanlagen :ein automatisiertes Stanzzentrum der Marke Trumpf und eine Laserschneidanlage der Marke Bystronic sowie über 2 CNC- gesteuerte Biegemaschinen zur Herstellung der Blechform. Zur Fertigung der maschinengeschweißten Komponenten gelangen bei ETESIA 4 Schweißroboter mit digitalen Achsen-Manipulatoren zum Einsatz.
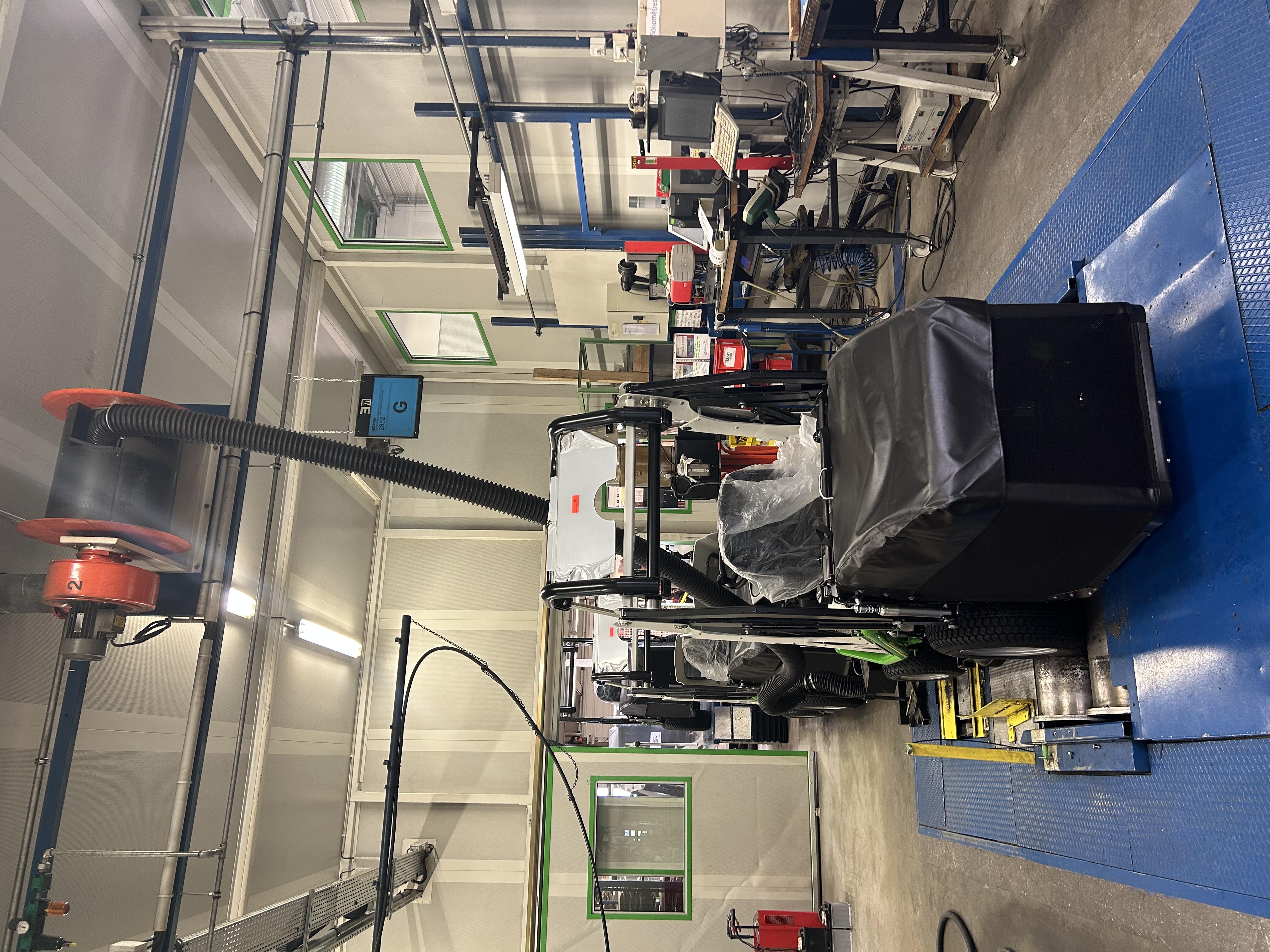
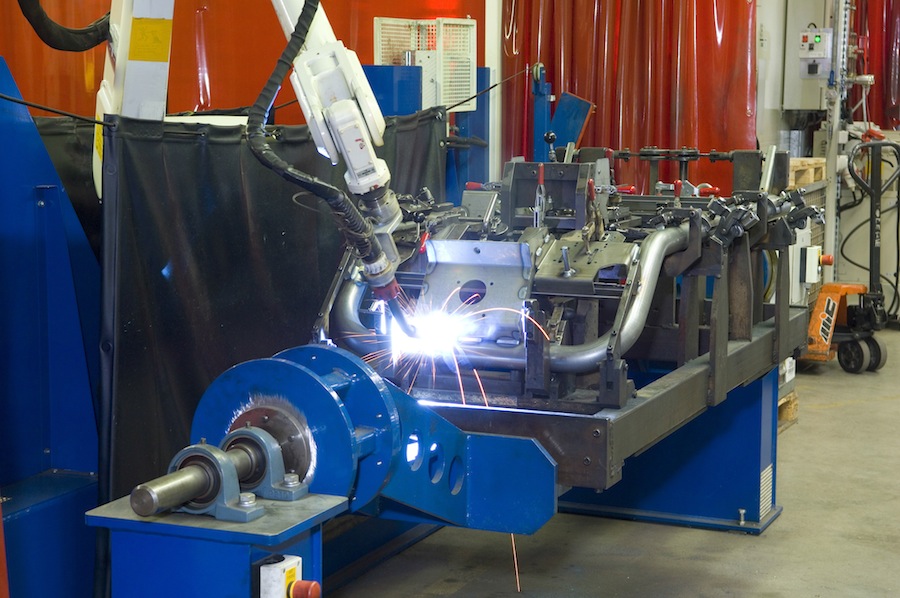
Der Montagebereich
Der Montagebereich besteht aus 3 Montagelinien, von denen jede einen Prüfstand beinhaltet, so dass die Qualität des Produkts vor der Auslieferung überprüft werden kann.
Die erste Linie wurde im Jahr 1989 eingeweiht. Hier erfolgt die Montage von Benzin-Aufsitzmähern mit einer Schnittbreite von 80 und 100 cm. Es handelt sich hierbei um ein Fließband in der Art der Automobilindustrie mit einer Länge von 100 m, das mit 10 selbstfahrenden Schlitten ausgestattet ist. Die Montage erfolgt in 2 Schichten mit jeweils 16 Mitarbeitern mit einer maximalen Tageskapazität von 60 Maschinen.
Die Kontrollkabine ist mit 2 Prüfständen zur elektronischen Datenerfassung ausgestattet. Damit können die technischen Eigenschaften jeder produzierten Maschine verfolgt und archiviert werden.
Die Montagelinie für Diesel-Rasenmäher ist ausschließlich für die Produktion von Profimodellen mit Dieselmotor und einer Schnittbreite von 100, 124 und 144 cm vorgesehen. Die Fließbandlänge beträgt 45 m, die aktuelle Tageskapazität erreicht je Schicht 8 Maschinen und liegt somit bei 16 Maschinen am Tag.
Die Kontrollkabine dieser Montagelinie ist einmalig in Europa: Dort werden unter anderen folgende Tätigkeiten ausgeführt: Reinigung des Hydraulikkreislaufs,Überprüfung auf Leckagen mittels UV-Lampen, Vornahme diverser Einstellungen. Alle Daten werden in einem IT-System gesichert, um deren Rückverfolgbarkeit zu gewährleisten.
Die letzte Linie dient der Montage des Biocut SKM und des Attila SKF mit einer Schnittbreite von 85 cm. Mit einer Länge von 30 m verfügt diese Linie über 8 Montageplätze mit einer Tageskapazität von 14 Maschinen. Die Abteilung interne Logistik unterstützt die Produktionstätigkeit und verfügt dazu über ein Wi-Fi-Netzwerk, das den gesamten Standort abdeckt. Dadurch werden mit Hilfe von Einbauten an den Hubwagen Materialverfolgung und Lagermanagement in Echtzeit ermöglicht. Eingehende Waren werden "online" erfasst. Dazu verfügt das Personal über Pocket-PCs.
Forschung und Entwicklung
Ein Akt der Neuschöpfung und des Willens. Die Gestaltung eines neuen Produkts ist nicht nur von Kreativität und Zielstrebigkeit geprägt, sondern stellt auch eine Herausforderung für die Zukunft des gesamten Unternehmens dar.
Dem Konzern Elmar WOLF ist die Neuentwicklung ein ständiges Anliegen. Vor diesem Hintergrund kann das Wirken von ETESIA in nur 2 Worten zusammengefasst werden: klein, aber im Hinblick auf Innovation führend.
Das Forschungszentrum ELMAR WOLF - CREW ist eine gemeinsame Unternehmung von Outils WOLF und ETESIA. Es deckt 5% des Umsatzes und 10% der Arbeitskräfte ab.
Seitens ETESIA gelangen 10 Ingenieure und Techniker zum Einsatz, die sich voll und ganz der Innovation und Leistungsfähigkeit professionell genutzter Aufsitzrasenmäher widmen.
Das Projektierungsbüro umfasst 17 CAD-Arbeitzplätze, an denen unter CATIA V5 gearbeitet wird. Das Management der technischen Daten erfolgt mit Hilfe einer PLM-Software (Product Life cycle Management).
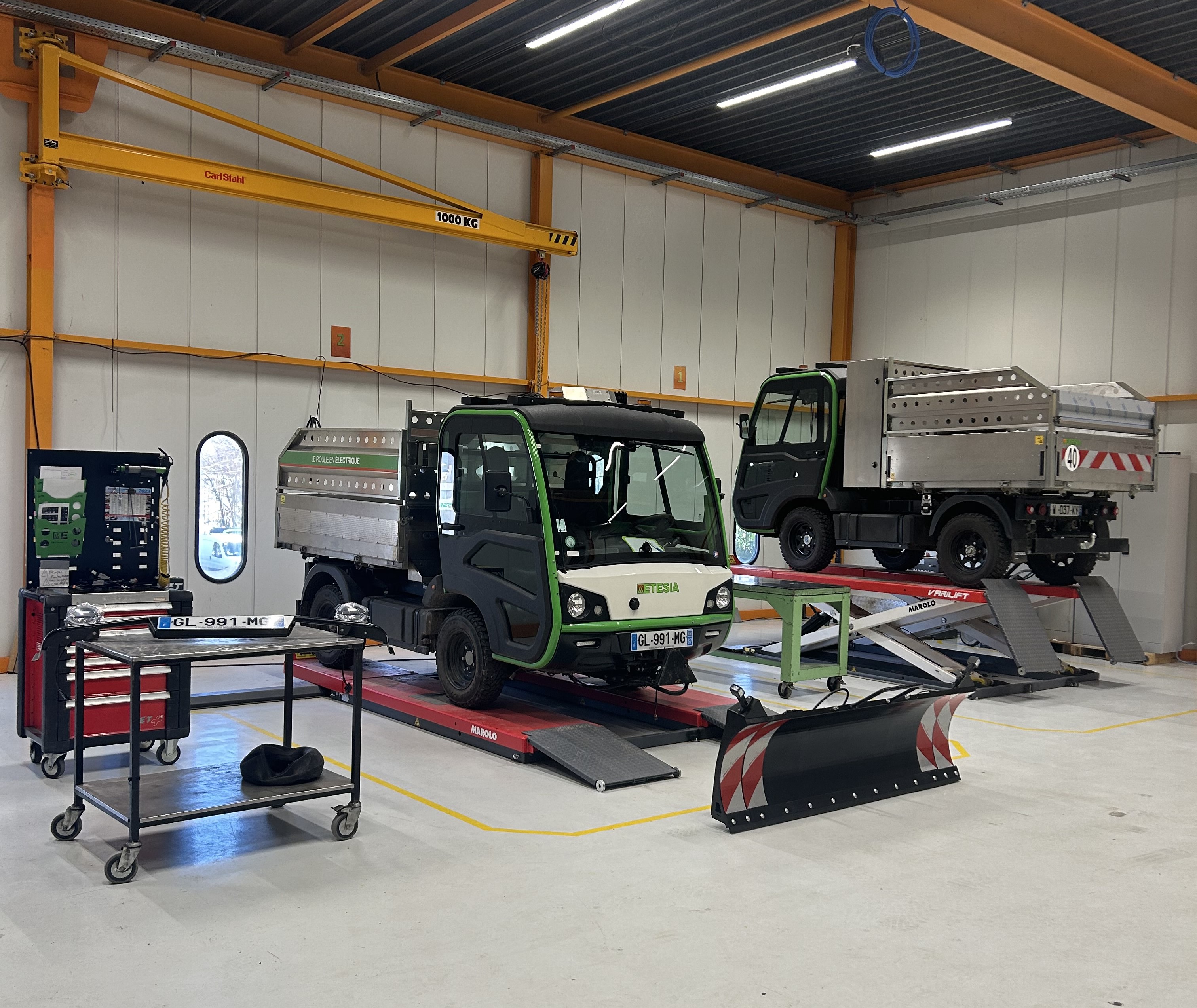
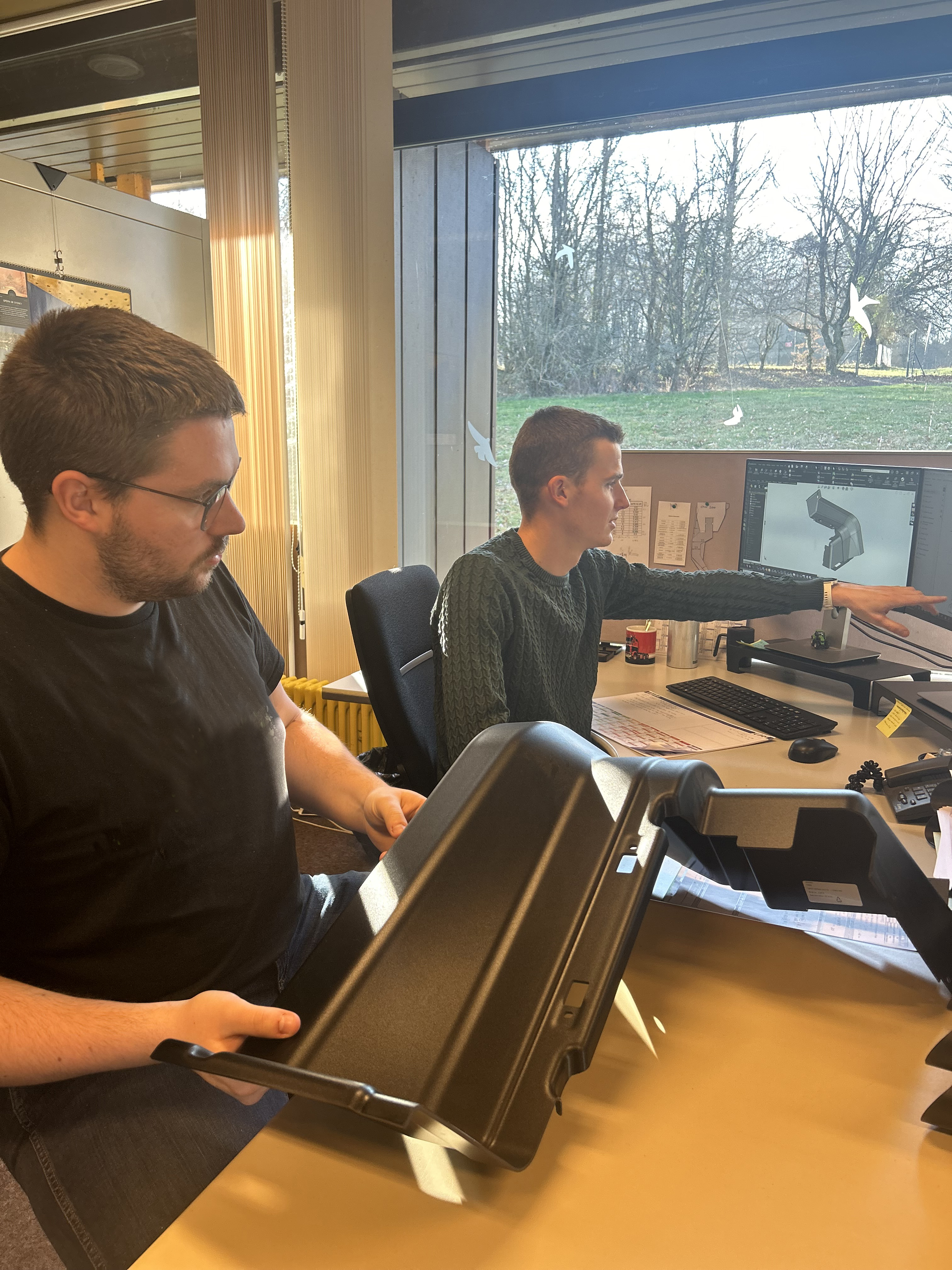
Eine weitere Software nach der FEM-Methode gestattet die Vornahme virtueller Simulationen, um bestimmte Teile oder Komponenten und sogar ganze Systeme vor Erstellung der Prototypen vergleichen und freigeben zu können. Die Prototypwerkstatt des CREW ist voll integriert. Sie verfügt über alle Werkzeugmaschinen, die zur Umsetzung der vom Projektierungsbüro festgelegten Funktionsmodelle erforderlich sind. Alle gemäß Normen geforderten und speziellen Tests, die die Sicherheit und Funktionalität der Produkte gewährleisten, werden intern abgesichert. So absolvieren die CREW-Teams jährlich 3.000 Prüfstunden in der Praxis und 30.000 Teststunden.